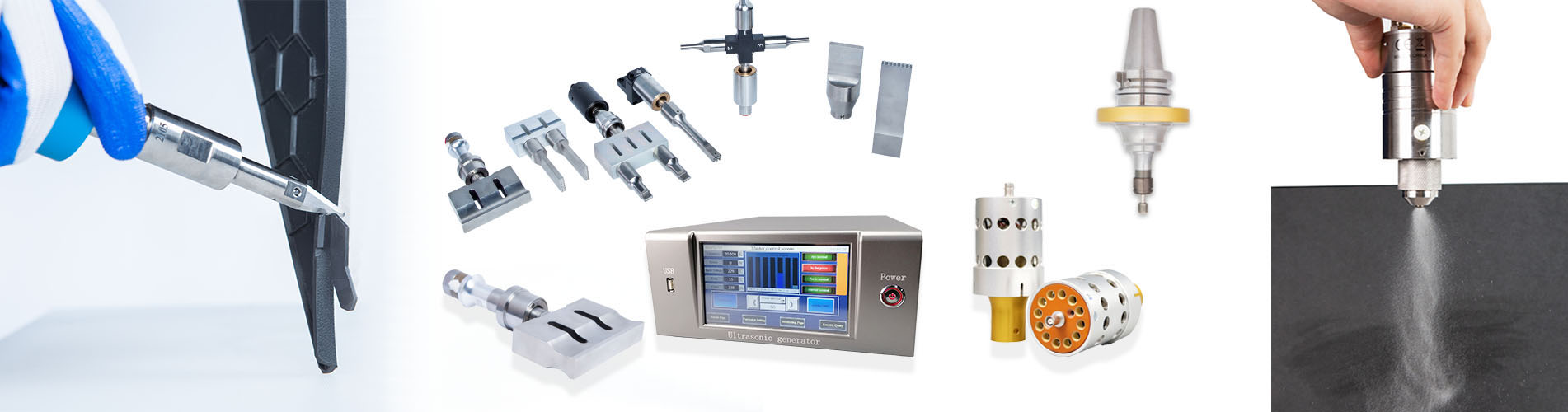
바이오디젤 생산
세 가지 일반적인 유형의 반응기가 바이오디젤 제작: 배치 반응기, 반연속 흐름 반응기 및 연속 흐름 반응기.
배치 프로세스는 저렴하며 훨씬 적은 초기 자본과 인프라 투자가 필요합니다. 유연하며 사용자가 공급원료 유형, 구성 및 수량의 변화를 수용할 수 있습니다. 배치 프로세스의 주요 단점으로는 낮은 생산성, 제품 품질의 더 큰 변동, 더 많은 노동력과 에너지 요구사항이 있습니다.
반연속 공정은 생산자가 보다 더 적은 양의 반응으로 시작한다는 점을 제외하고는 배치 공정과 유사합니다 용기는 유지되고 계속해서 재료를 추가합니다 그릇이 가득찼습니다. 이 프로세스는 노동 집약적이며 일반적으로 사용되지 않습니다.
연속 에스테르 교환 대용량 상업적 생산 때문에 이들 프로세스 결과 일관된 제품 품질과 낮은 자본 및 운영 비용 per 제품의 단위 가장 일반적인 유형의 연속 흐름 반응기는 연속 교반 탱크 반응기. 다른 유형의 연속 흐름 초음파 반응기 및 초임계 반응기를 포함하여 반응기도 상업적으로 사용됩니다. 이것들 대체 절차는 반응 속도를 높일 수 있습니다.
아이다호 대학교 연구에 따르면 정적 혼합 반응기와 반응성 증류가 바이오디젤 처리하지만 이들 공정은 아직 바이오디젤 상업적으로.
배치 반응기는 단순히 어떤 유형의 교반 장치가 장착된 탱크일 수 있습니다. 탱크는 공정을 위한 반응물 (여기서는 오일, 알코올 및 촉매)로 채워지고 교반기는 일정 시간 동안 작동됩니다. 필요한 시간이 경과한 후 반응기의 내용물을 배출하고 추가 처리합니다.
배치 반응기의 주요 특징은 미반응 물질이 반응하도록 하고 나중에는 물질이 반응하게 됩니다. 그 즉, 배치 반응기에는 우연히 보는 시간에 따라 다양한 유형의 물질이 포함됩니다.
배치 반응기는 일반적으로 소형 바이오디젤 생산 식물. 회분식 공정의 단점은 생산량을 늘리기 위해 공장의 물리적 크기를 비례적으로 늘려야 할 수도 있다는 것입니다. 대조적으로, 때 연속 흐름 공정을 사용하면 일반적으로 식물의 공급 속도를 높이거나 반응 시간을 단축하여 생산 능력을 높입니다.
가장 일반적인 연속 흐름 바이오디젤 생산은연속 교반 탱크 반응기 (CSTR). 언뜻 보기에 그림 1에 표시된 것과 같은 CSTR은 배치 반응기와 동일한 것처럼 보입니다. 사실, 종종 실제 반응기는 동일할 수 있지만 연속 흐름 에서 반응기를 설정하려면 추가 제어가 필요합니다. 시스템. 일부 지속적인 흐름 플랜트는 배치 또는 연속 모드로 작동할 수 있습니다.
CSTR에서 반응물은 연속적으로 추가되고 생성물 (미반응 반응물을 포함한 다양한 화학 물질의 혼합물 ) 지속적으로 철수. 균일한 화학 조성과 온도를 보장하기 위해 적절한 교반이 필요합니다. 지속적인 흐름 프로세스에는 일반적으로 복잡한 프로세스 제어와 제품 품질의 온라인 모니터링이 필요합니다.
언제 CSTR 정상 상태에서 연속적으로 작동되며 이상적으로는 관련된 모든 화학 물질의 농도가 반응기의 어느 곳에서나 항상 거의 일정해야 합니다. 실제로 이 이상적인 상태는 거의 달성되지 않습니다. 따라서 완전한 반응을 보장하기 위해 작동 매개변수를 조정해야 합니다.
때로는 보다 하나의 반응기가 사용됩니다. 이 시스템에서 약 80%의 알코올과 촉매가 첫 번째 단계 CSTR. 그런 다음, 반응 스트림은 두 번째 CSTR에 들어가기 전에 글리세롤 제거 단계를 거칩니다. 알코올과 촉매의 나머지 20%가 이 반응기에 추가됩니다. 이 시스템은 더 적은 알코올을 사용하는 가능성과 함께 매우 완전한 반응을 제공합니다 한단계 시스템.
초음파는 분리되는 경향이 있는 액체를 혼합하는 데 유용한 도구입니다. 바이오디젤 생산, 식물성 기름/동물 지방과 알코올, 특히 반응 초기에. 초음파는 강한 혼합을 일으켜 반응이 훨씬 더 빠른 속도로 진행될 수 있도록 합니다.
초음파는 에너지를 유체로 전달하고 격렬한 진동을 생성하여 캐비테이션 거품. 기포가 터지면서 유체의 급격한 수축이 일어나며 거품이 있는 부분에 재료가 섞이게 됩니다. 액체에서 이러한 고에너지 작용은 반응 혼합물의 반응성을 상당히 증가시키고 온도 상승 없이 반응 시간을 단축할 수 있습니다. 사실, 이 반응은 주변 온도 또는 그보다 약간 높은 온도에서 달성할 수 있습니다. 왜냐하면 혼합물을 가열할 필요가 없으므로 에너지를 절약할 수 있습니다.
연구에 따르면 초음파는 바이오디젤 (예: Sarma et al., 2008; Hanh et al., 2008; Teixeira et al., 2009). 초음파 처리 결과 유사한 수율 바이오디젤 기존의 교반 탱크에 비해 훨씬 짧은 반응 시간으로 절차.
초음파는 하나 또는 두 개의 초음파 프로브만 필요할 수 있는 소규모 생산자 (최대 2백만 갤런 연간 용량)에게 좋은 선택이 될 수 있습니다 당 원자로 용기 그러나 대규모 처리에서 초음파를 사용하는 것은 어려울 수 있습니다. 때문에 많은 초음파 프로브 반응물 혼합물의 모든 영역에 도달하는 데 필요합니다.
전통적인 바이오디젤 생산에는 촉매가 필요합니다 (일반적으로 나트륨 또는 칼륨 수산화물) 에스테르 교환 반응을 완료하기 위해 반응. 반응 후 촉매를 제거하여 연료 품질을 보장해야 합니다. 이 때때로 문제가 될 수 있습니다. 까지 촉매 요구 사항을 피하십시오, 트랜스에스테르화 촉매가 없는 "초임계" 과정.
~에 따르면 화학공학개론 열역학,유체의 임계점은 임계 온도와 임계 압력으로 정의됩니다. " 순수한 화학종이 증기/액체 평형에 존재하는 것으로 관찰되는 최고 온도 및 최고 압력" (Smith et al., p. 64).
~에서 초임계 상태,액체와 증기 사이의 상 경계가 사라지기 시작하고 물질은 액체와 증기의 성질을 모두 가지고 있습니다.
언제 에스테르 교환 하는 동안 메탄올 (일반적으로 300°C 및 40 MPa/5800 psi 이상)의 초임계 상태에서 식물성 기름 또는 동물성 지방은 메탄올에 용해되어 단일상을 형성합니다. 그런 다음 반응이 일어나서 촉매 없이 몇 분 안에 완료됩니다.
초임계 공정은 시스템에서 물과 유리 지방산을 허용하며 기존 공정에서 일반적으로 발생하는 비누 형성이 제거됩니다(Demirbas, 2006; van Kasteren 및 Nisworo, 2007; Saka 및 Isayama, 2009).
이후 초임계 상태는 매우 높은 온도와 압력을 필요로 하므로 비용이 많이 들 수 있습니다. 그럼에도 불구하고 대형 바이오디젤 생산자는 이 프로세스가 비용 효율적이라는 것을 알 수 있습니다. ~ 때문에 반응이 너무 빨리 일어나기 때문에 생산자는 상대적으로 작은 반응기와 제한된 공간으로 많은 양을 만들 수 있습니다.
정적 믹서 나선 모양 난류를 촉진하는 튜브나 파이프와 같은 인클로저 내의 내부 부품 그들 움직이는 부분이 없고 사용 및 유지 관리가 쉽고 정상적인 조건에서 쉽게 섞이지 않는 액체를 혼합하는 데 매우 효과적입니다.
바이오디젤 식물성 기름과 알코올로부터의 생산은 처음에 식물성 기름의 알코올 용해도에 의해 제한됩니다 (Van Gerpen 및 Knothe, 2005). 정적 혼합기를 사용하여 그들 원자로 용기에 들어가세요. 정적 믹서 자체 원자로 용기로도 사용되나요? 연속 흐름 바이오디젤용 반응기 생산 ( 톰슨과 그, 2007 ).
결과는 정적 혼합 반응기가 바이오디젤 생산, 그리고 제품 ASTM D6584 사양을 얻었습니다. 다른 반응기 구성과 마찬가지로 온도와 촉매 농도가 생성물 수율에 상당한 영향을 미쳤습니다. 완전한 에스테르 교환 반응에 가장 유리한 조건 60°C 그리고 1.5% 30분 동안 촉매제 따라서 바이오디젤 식물성 기름과 알코올로 만든 조제품
유사한 공정이 때때로 상업적으로 사용되지만 바이오디젤 프로세서가 상업화되지 않았습니다.
반응성 증류 (RD) 하나의 장치에서 화학 반응과 생성물 분리가 동시에 일어나는 화학 장치 작업입니다. 반응기와 분리 장치의 고전적인 조합에 대한 효과적인 대안입니다.
반응성 증류는 상황에서 일반적인 화학 공정입니다 반응이 역전될 수 있습니다 쉽게. RD 기술은 반응 구역에서 반응 생성물을 제거하여 반응이 역전되는 것을 방지하고 전체 전환율을 개선합니다.
RD 시스템은 하나에서 다음으로 가는 구멍이 있는 수많은 챔버로 구성되어 있습니다. 재료를 첫 번째 챔버에 넣고 혼합물이 각 연속 챔버에 들어감에 따라 반응이 진행되어 마지막 챔버에서 반응이 완료됩니다. RD 에는 포장 및 트레이 열을 모두 사용할 수 있습니다. 응용 프로그램; 그러나 균질한 반응 시스템에는 트레이 컬럼이 선호됩니다 더 큰 액체 보유량과 상대적으로 더 긴 체류 시간
반응성 증류 시스템은 바이오디젤 생산 때문에 RD 프로세스가 복잡한 경향이 있습니다. 그러나 복잡성은 다소 최소화됩니다 바이오디젤 몇 가지 이유로 생산. 메탄올과 지방산 에스테르의 끓는점 차이 (바이오디젤) 이 의 분리가 너무 커서 두 개의 스트림이 매우 쉽게 됩니다. 왜냐하면 에스테르 교환 반응은 액상에서만 발생하며, 반응 시간은 총 액체 보유량과 반응물의 공급 속도에 의해 설정됩니다.
국립 첨단 교통 기술 연구소(National Institute of Advanced Transport Technology)가 후원하는 아이다호 대학에서 수행된 연구에 따르면 (NIATT) (그 et al., 2005, 2006, 2007), RD 반응기 시스템은 배치 및 기존의 연속 흐름 프로세스: 1) 짧은 반응 시간 (10 ~ 15 분) 및 더 높은 단위 생산성 (7 ~ 9갤런 당 갤런 반응기 부피 당 시간), 이는 상업적 생산에서 매우 바람직함 2) 훨씬 낮은 초과 알코올 요구량 (대략 3.5:1 몰), 이는 다운스트림 알코올 회수 및 운영 비용의 노력을 크게 줄임; 그리고 3) 더 작은 크기와 알코올 회수 장비의 필요성 감소로 인해 자본 비용이 낮습니다.
이전의 :
파워 초음파가 초 임계 유체 추출 보조다음 :
초음파 용접© 저작권: 2025 Hangzhou Altrasonic Technology Co.,Ltd 판권 소유
IPv6 네트워크 지원